By Lori Widmer, The Rough Notes Company
Original article published by RoughNotes and available here.
For Gabriel Glynn, COSS, chief executive officer of MākuSafe®, of West Des Moines, Iowa, a visit with his father turned into a brand-new way to approach worker safety.
Glynn’s father, a retired safety manager, had spent a career managing the safety efforts for a facility employing around 2,000 workers. Glynn had asked his father to explain what he did for a living. “He said, ‘I wait for something bad to happen, I figure out why it happened, I put a plan in place so that it doesn’t happen again, and I fill out a whole bunch of paperwork as to why it happens. Then I deal with the next bad thing.’ Then he said something really interesting to me: ‘If I get lucky enough, enough bad things happen that I have enough data that I can start to see a pattern, and I can try to get out in front of something.’”
To Glynn, that approach was far too reactive when dealing with people’s safety. It was also a problem he wanted to solve. Glynn, whose entrepreneurial background includes starting technology and service-based companies, decided to contact former customers and have conversations with their safety teams. Their answers were the same: When an incident occurred, the safety people would examine the hows and figure out the whys, then move forward with a revamped safety approach.
“I realized safety is so reactionary, but there has to be a way that we can gather the right kind of data that provides us the clues that somebody is at risk more than another person.”
Enter MākuSafe, a connected worker-wearable technology and safety data analytics solution. The industrial wearable safety technology monitors workers’ environmental exposure, human motion, location conditions, and incident data as well as provides ongoing data that can help safety professionals build a profile into each worker’s movements and physical reaction to work conditions and requirements.
Individual worker data
What sets MākuSafe apart from other wearable technologies, says Glynn, is how it records and measures each worker’s unique experience. He explains why that’s important: “If you and I are on a jobsite, and we’re working ten feet apart from each other, there’s a machine between us. That exhaust is coming off at me, the sound is coming off at you. You’re loading stuff in one side, I’m pulling it out the other side. At the end of a ten-hour shift, what we’ve experienced, even though we were just ten feet apart from each other, is completely unique from each other.”
When employers can see the impact of both environment and motion on each worker, they are better equipped to intervene before injury occurs. “We’re not just drawing general conclusions about work,” says Glynn. That’s more accurate because, Glynn points out, movement varies from person to person. Factors like gender, size, prior injury, and genetic predispositions all impact how a person moves and responds to movement and environment.
MākuSafe provides real-time monitoring and notification, measuring ergonomics, including repetitive motion, musculoskeletal movement and injury potential, and environment, including air quality, air pressure, heat, sound octave, and ambient light.
Another feature: a push-to-talk communication link, which allows workers to record a message up to 15 seconds in length that allows them to alert supervisors within seconds to problems, near accidents, and other on-site observations. The supervisor can then assign and track the resolution of issues through the online platform.
It can also illustrate the results of a more proactive safety program. “At the end of the year, a safety person can stand in front of leadership and say, ‘Yes, we had zero recordable accidents this year. But let me tell you, we found 78 hazards in our facility that were reported to us. We responded and remediated those hazards in less than 24 hours in all cases but two, and here’s why on these other two. And here’s all the documentation, and here are the maintenance records for the things that were fixed or changed.’ It becomes a powerful tool, and the advocacy for the safety team to be able to show what they’re doing from a productivity standpoint when nothing bad is happening.”
What customers say
Joe McGettigan, senior risk control consultant with Conner Strong & Buckelew, an insurance, benefits and risk consulting firm, worked recently with a large logistics company to help them locate a wearable technology solution so that they could monitor ergonomic risks.
The client, a third-party logistics provider, was looking to reduce injuries and better understand what factors were contributing to musculoskeletal disorders within their facilities. They were looking for a technology that could measure the intensity of worker energy outlay, the impact on the worker, and how such movement would impact the worker over time.
But first, the client had to locate the right product. The process of choosing was a little disconcerting. “The companies seem to over-promise on the type and/or precision of the information that they could deliver,” McGettigan says.
Not so with MākuSafe, he says. Their “more pragmatic, more intellectually honest approach in terms of what they were actually measuring and what could be done with the information” appealed to the client, McGettigan says. MākuSafe’s movement analysis was what interested McGettigan’s client. “MākuSafe openly said, ‘We know that something is happening, but we don’t know what is happening, so we need a human to go out and look at the tasks to know exactly what’s going on, and come up with any specific solutions.’ This approach was in line with our general philosophy, so we worked toward a pilot program.”
The client started with selecting which site locations would be part of the pilot program, says McGettigan. “Sites that had historically higher injury rates were chosen for the pilot and subsequent installations.”
Once the pilot sites were chosen, the product was implemented. The onboarding process, says McGettigan, went well. “Once the more complicated information technology issues were worked out at each site, the onboarding experience was actually pretty smooth. MākuSafe personnel did their hardware and software installations while we were ‘installing’ other aspects of the ergonomics program with training. This process developed into a good partnership in addressing ergonomic issues at each of this client’s sites.”
At present, the client is piloting 120 MākuSafe wearables at three locations, focusing on those workers who perform materials-handling tasks. So far, so great. Data obtained by the wearable devices have given the client valuable insight into injury potential.
Supported by the behavior-based safety protocols and customized lifting techniques training implemented by McGettigan’s team, the client’s quarterly injury results showed a 74% decrease in injuries at all pilot sites.
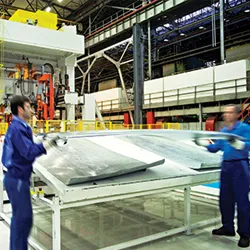
There were other benefits, as well. The company has seen an organizational improvement in safety and technology. Also, the company is able to be more transparent with employees and how the data gathered is used. In fact, Glynn says that companies working with MākuSafe must have the right goals in mind. “We will not move forward with a company if we feel they’re going to use the data in any way that is punitive to the worker.”
For the client to be successful using MākuSafe, McGettigan says it focused on the right outcome. “The main lesson was that this common-sense approach was accurate and worked well getting good results. Strong, regular, consistent follow-up was also a key to success,” says McGettigan.
He also recommends that companies understand their role in the process. “Wearable technologies are only as good as the systems into which they are installed,” says McGettigan. “Having good surveillance data is a good thing, but if the people or the systems aren’t equipped to do something with the information, the effort will fold. Insurers and brokers need to be ready to walk with their clients to support any initiative they seek to install.”
Taruja Deshmukh, vice president of InsurTech Solutions Managers for Conner Strong & Buckelew, says that agents and brokers can help secure a more successful technology experience for clients. “Having an advocate for innovation in safety within all parties—client, broker, and carrier—is instrumental in delivering a successful outcome,” she says. “Especially within the client, having a champion that understands the solution and the boundaries of the technology is critical when it comes to communicating expectations to employees, setting up training, following through on feedback and ultimately applying the information gained.”
Monday, April 15, 2024